Recognizing the Relevance of Welding Inspection Madison in Building
Discovering Advanced Tools and Approaches for Accurate Welding Examination
In the realm of welding evaluation, the pursuit of accuracy and integrity is extremely important, stimulating the growth of innovative tools and approaches. Laser scanning developments and computerized assessment systems, furnished with man-made intelligence, are redefining the landscape by reducing human error and enhancing safety actions.
Ultrasonic Checking Innovations
Ultrasonic screening advancements frequently stand for the forefront of innovations in welding assessment technologies. These advancements have dramatically improved the capability to discover and assess stoppages within bonded frameworks, making certain enhanced integrity and safety.
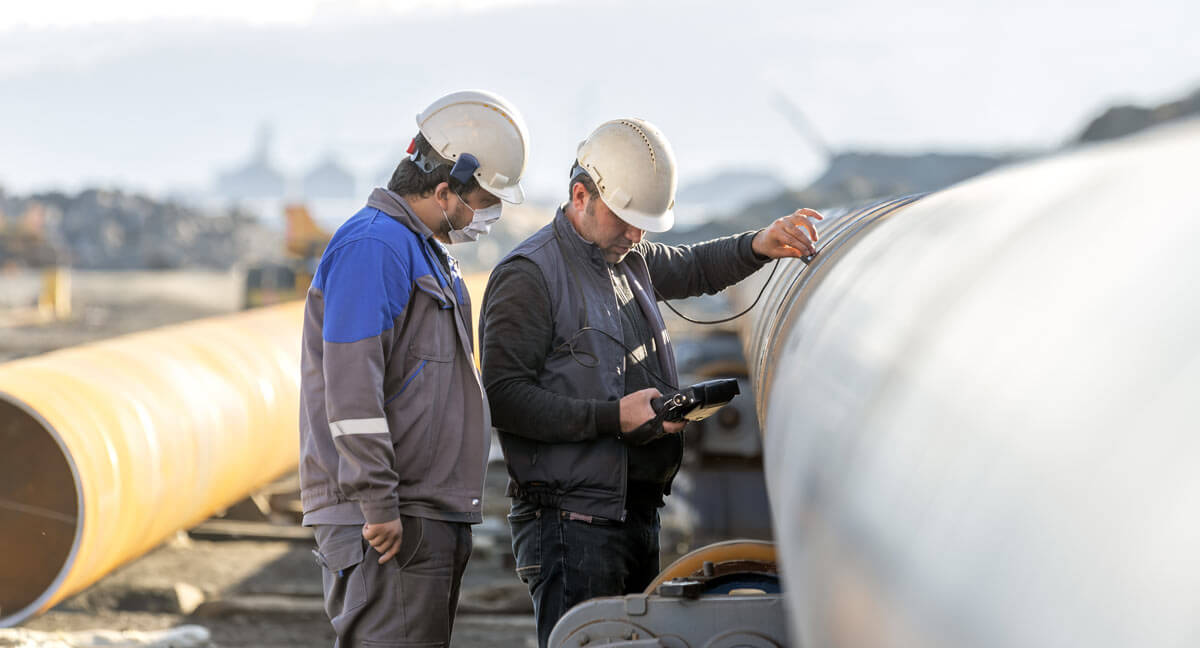
In addition, developments in software algorithms for information analysis have improved the accuracy of flaw discovery and sizing. Automated ultrasonic testing systems now offer high-resolution imaging, making it possible for in-depth evaluations of weld high quality. These systems are often incorporated with advanced visualization tools, which assist in the analysis of results.
Radiographic Evaluation Methods
While ultrasonic screening advancements have established a high requirement in non-destructive evaluation, radiographic evaluation methods remain to play an essential duty in welding evaluation by supplying one-of-a-kind understandings right into material stability. Radiographic screening (RT) employs using X-rays or gamma rays to permeate materials, creating a radiograph that aesthetically stands for the internal structure of a weld. This imaging ability is invaluable for spotting subsurface problems such as porosity, inclusions, and splits that might not be visible through surface area evaluations.
The process involves positioning a radiation resource on one side of the weld and a detector on the opposite side. Variants in material thickness and thickness impact the attenuation of the rays, generating a different image that precisely marks problems. RT is particularly useful for checking thick sections and intricate geometries where other methods might drop short.
Regardless of its efficiency, radiographic evaluation has to be carried out with strict adherence to safety and security procedures as a result of the harmful nature of ionizing radiation. Moreover, the analysis of radiographs requires knowledgeable workers, as the quality of the evaluation straight affects the reliability of the examination. Recurring developments in digital radiography are improving photo quality and analysis efficiency, reinforcing RT's vital function in making certain weld top quality.
Laser Scanning Advances
Embracing laser scanning modern technology in welding examination has transformed the assessment of weld high quality and integrity. Unlike typical examination strategies, laser scanning supplies rapid information purchase, substantially improving the efficiency and precision of weld assessments.
Laser scanning advances have actually led to considerable improvements in identifying and discovering surface area defects such as porosity, absence of fusion, and undercuts. The high-resolution data enables examiners to execute extensive evaluations, ensuring that welds satisfy rigorous industry requirements. This approach sustains the development of digital records, assisting in lasting quality assurance and traceability.
Furthermore, laser scanning innovation incorporates flawlessly with software solutions developed for automated flaw discovery and analysis. The resultant information can be conveniently shared and assessed, advertising joint decision-making procedures. As sectors proceed to require greater requirements for weld high quality, laser scanning stays at the leading edge, using unrivaled precision and effectiveness in welding assessment.
Automated Assessment Solutions
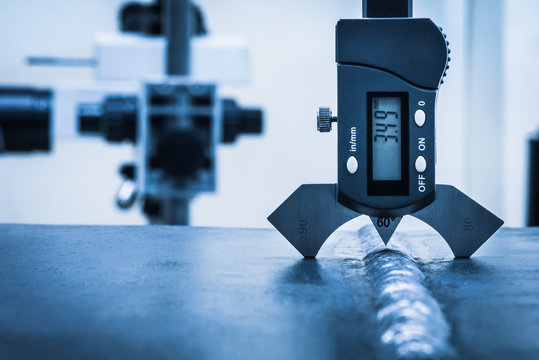
Automated assessment systems use the advantage of consistency, removing human error and subjectivity from the evaluation process. They are designed to run in numerous atmospheres, from production floorings to remote area sites, guaranteeing comprehensive insurance coverage. Welding Inspection Madison. These systems can be set to stick to specific welding criteria and requirements, providing thorough records and documentation for quality assurance functions
Furthermore, the integration of cloud-based systems facilitates the storage space and analysis of substantial amounts of examination data. This enables pattern analysis and predictive upkeep, enabling manufacturers to attend to potential issues prior to they escalate. The adoption of computerized evaluation see it here systems is a crucial step towards improving the integrity and efficiency of welding processes in commercial applications.
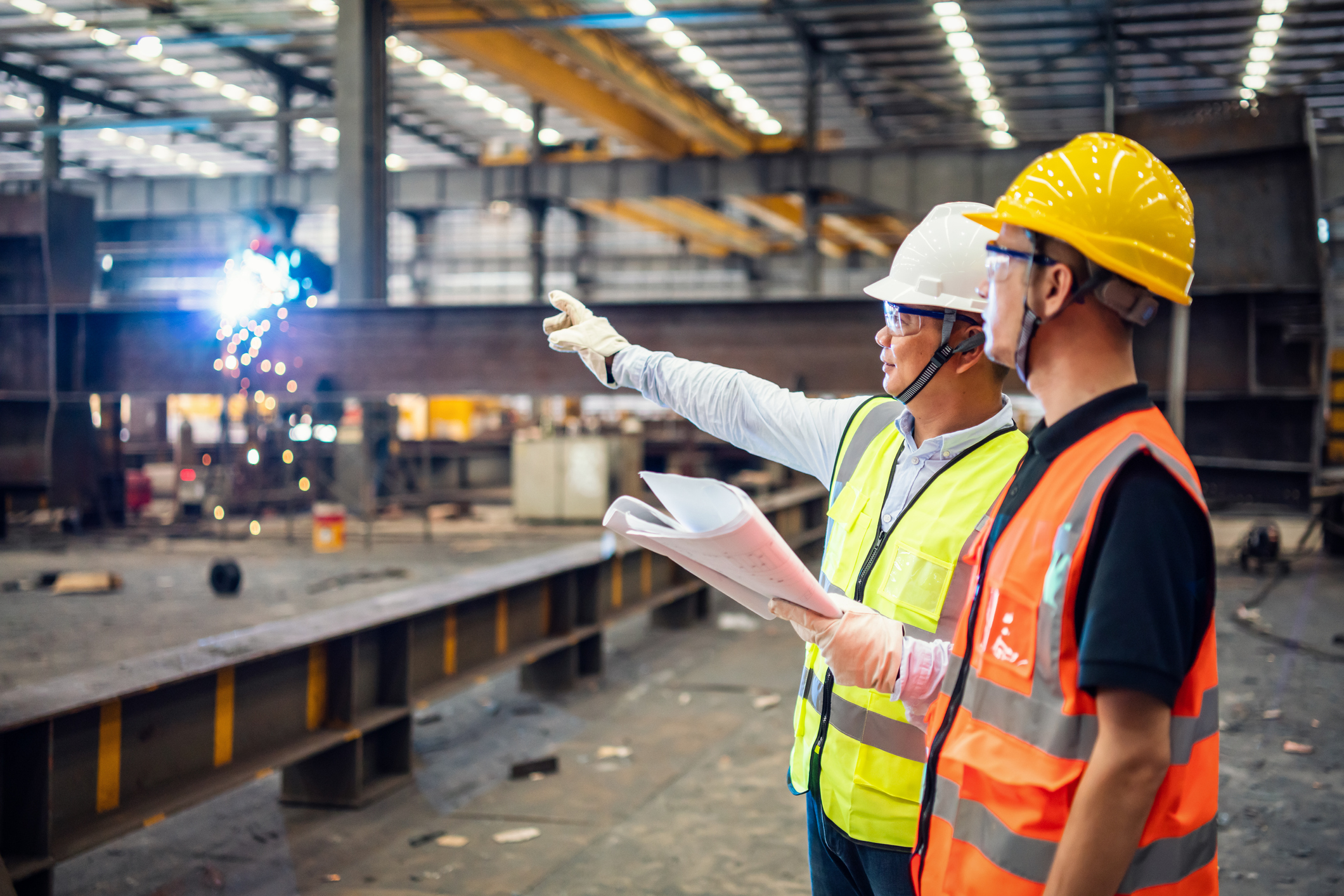
Enhancing Security and Effectiveness
A considerable facet of boosting safety and security and efficiency in welding inspection lies in the combination of ingenious technologies that streamline operations and reduce risks. The fostering of sophisticated non-destructive screening (NDT) techniques, such as ultrasonic testing, phased range ultrasonic testing (PAUT), and radiographic testing, plays a critical function in guaranteeing architectural integrity without endangering the safety and security of the workers included. These strategies enable my response detailed assessments with marginal downtime, decreasing potential risks connected with conventional approaches.
Furthermore, the execution of real-time data analytics and artificial intelligence formulas has actually transformed the way inspection information is analyzed. By utilizing predictive analytics, prospective flaws can be recognized prior to they show up into critical failures, making sure timely treatments and upkeep. This proactive method substantially boosts operational effectiveness and security in welding processes.
Furthermore, remote examination technologies, including drones and robot spiders equipped with high-resolution electronic cameras, enable assessors to examine hard-to-reach locations without revealing them to harmful conditions. This not just enhances assessment precision however also decreases human danger. By leveraging these advanced devices and methods, sectors can accomplish greater security standards and functional efficiency, eventually leading to even more lasting and reputable welding inspection methods.
Conclusion
The assimilation of innovative devices and approaches in welding inspection significantly enhances problem detection and guarantees structural stability. These innovations not just raise examination performance yet additionally add to improved safety and quality guarantee in commercial welding applications.

Ultrasonic testing developments frequently stand for the leading edge of advancements in welding examination modern technologies.While ultrasonic testing innovations have actually set a high requirement in non-destructive evaluation, radiographic inspection strategies continue to play an integral duty in welding evaluation by offering special insights right into material stability.Embracing laser scanning modern technology in welding evaluation has reinvented have a peek at this site the evaluation of weld quality and stability. As industries continue to require higher requirements for weld quality, laser scanning stays at the center, providing unparalleled precision and efficiency in welding assessment.
Automated inspection systems provide the benefit of consistency, getting rid of human mistake and subjectivity from the inspection procedure.